PROCEDIMIENTOS DE FABRICACIÓN
Aquí hablaremos de tres procesos de fabricación que hemos seleccionado:
CORTE POR PLASMA
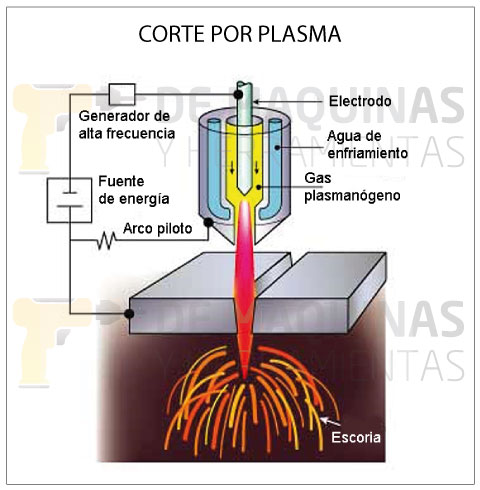
TIPO DE PROCEDIMIENTO:
El corte por plasma es un proceso de fabricación que forma parte de un tipo de corte denominado corte térmico en el cual existe pérdida de material. Utiliza un chorro de alta velocidad de gas ionizado que se envía desde un orificio de constricción. La alta velocidad del gas ionizado (que es el plasma) conduce la electricidad desde la antorcha de plasma a la pieza de trabajo. El plasma calienta la pieza de trabajo, fundiendo el material y finalmente el flujo de alta velocidad del gas ionizado sopla mecánicamente el metal fundido, rompiendo el material.
MATERIALES EN LOS QUE SE UTILIZA:
Puede usarse en ferrosos y no ferrosos, en oxidados, pintados o en malla, al igual que en cualquier tipo de metal conductor, acero suave, aluminio y acero.
TIPO DE PIEZAS QUE SE OBTIENEN:
El corte por plasma es utilizado en la industria de la automoción para fabricar chasis y bastidores. También se utiliza en la industria de la construcción para cortar y fabricar grandes vigas y otros productos de chapa metálica, al igual que es utilizado en otras industrias como la minera y la naval para fabricar y reparar sistemas de tuberías y ventilación por ejemplo.
MAQUINARIA NECESARIA:
El equipo básico de cortado de plasma contiene los siguiente utensilios:
Antorcha para aplicar el plasma. Esta contiene un electrodo y una zona por donde pasa el gas, en el cual se puede utilizar argón, hidrógeno, nitrógeno, oxígeno, aire o una mezcla del conjunto. El más utilizado es, sin embargo, el nitrógeno, ya que proporciona cortes de mejor calidad y reduce el deterioro de la boquilla de la antorcha.
Bombona de aire comprimido.
Máquina de corte por plasma.
IMPACTO AMBIENTAL:
En los distintos procesos de producción de acero mediante este proceso quedan desechos de material como son el hollín, la merma, la chatarra, la rebaba, la emisión de gases por la soldadura y corte, líquidos desechables de soluble, además de otros aspectos que pueden afectar directamente a los trabajadores como el ruido, humos, el sofocante calor, los sobrantes y desperdicios generados por la soldadura, la pulidora.
ANÁLISIS HISTÓRICO:
Su origen se remonta a 1954, cuando se descubrió que aumentando el caudal de gas y disminuyendo la abertura de la boquilla en la soldadura TIG se obtiene un haz de plasma capaz de cortar metales.
Como dato curioso, se puede mencionar la existencia de la soldadura por plasma, la cual es una variante de la soldadura TIG.
Se diferencia de esta en que se trabaja a temperaturas más altas para producir el plasma y la boquilla de la pistola es más estrecha.
La zona de impacto es menor que en la soldadura TIG, por lo que es buena para chapas de poco espesor.
PERSPECTIVAS FUTURAS:
El corte plasma ha sufrido constantes desarrollos y mejoras haciendo que hoy en día existan diferentes tipologías y configuraciones de máquina. En su constante evolución el papel de los gases industriales ha adquirido cada vez más complejidad y relevancia, no sólo por su fuerte influencia en la buena marcha del proceso tanto a nivel productividad como de calidad de corte, sino por la gran cantidad de gases que pueden formar parte del proceso. También se puede mencionar la existencia de robots los cuales utilizan este proceso de fabricación de forma independiente.
http://www.directindustry.es/prod/haco-atlantic-inc/product-190274-1869319.html
EMPRESAS QUE LO UTILIZAN:
Ejemplos de empresas que utilizan este proceso pueden ser:
EWM AG
EBNER GMBH & CO KG
Kjellberg Finsterwalde
ELECTROEROSIÓN POR HILO
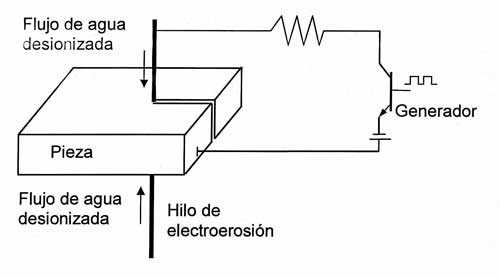
TIPO DE PROCEDIMIENTO:
El corte por electroerosión por hilo es un proceso de fabricación que forma parte de un tipo de corte denominado corte por arranque de viruta en el cual existe pérdida de material. Es un proceso de mecanizado mediante el cual se utiliza un hilo de metal para cortar un contorno programado en una pieza. El hilo siempre atraviesa la pieza. Antes de empezar a mecanizar, es necesario realizar un agujero en la pieza. O bien, el mecanizado debería entonces empezar en el borde de la pieza. Desde que el hilo puede ser inclinado, es posible cortar piezas cónicas o de diferentes perfiles desde la superficie hasta el final de la pieza. El hilo se basa generalmente en aleaciones de cobre y diámetros desde 0.02 hasta 0.33mm.
MATERIALES EN LOS QUE SE UTILIZA:
Todos los materiales que se someten a mecanizado por electroerosión deben ser eléctricamente conductores o semiconductores, sin zonas de corte no conductoras. Estos materiales incluyen aceros endurecidos y con tratamiento térmico, carburo, diamante policristalino, titanio, aceros laminados en caliente y en frío, cobre, bronce y aleaciones de altas temperaturas.
TIPO DE PIEZAS QUE SE OBTIENEN:
La electroerosión se utiliza para producir piezas muy pequeñas y precisas, así como grandes piezas tales como matrices de estampado para automóviles y componentes para el fuselaje de aviones. Por citar algunos ejemplos, se pueden mencionar:
Punzones y matrices de corte.
Matrices para plástico.
Matrices metálicas para pulvimetalurgia.
Matrices de extrusión y de embutición.
Prototipos, pequeñas series, piezas de recambio.
Plantillas.
Calibres.
Levas de disco.
Herramientas de troquelado de corte fino y normal.
Electrodos para electroerosión convencional.
MAQUINARIA NECESARIA:
Los equipos de electroerosión tienen una serie de componentes básicos y que, a grandes rasgos, podrían estructurarse en:
Electrodo.
Pieza de trabajo.
Fluido dieléctrico.
Sistema de filtrado y bombeo de dieléctrico.
Generador de corriente eléctrica.
Sistema de movimiento del electrodo o mecanismo de avance.
IMPACTO AMBIENTAL:
La mayor desventaja del proceso de electroerosión por hilo a destacar es su alto consumo de energía, la cual, a su vez, no es posible reutilizarla.
ANÁLISIS HISTÓRICO:
El origen del mecanizado por electroerosión se remonta a mediados del siglo XVIII, cuando se descubrió el efecto erosivo de las descargas eléctricas. Casi 200 años después y en plena Segunda Guerra Mundial, los científicos soviéticos B. y N. Lazarenko aprovecharon ese efecto con el objeto de desarrollar un proceso controlado para el mecanizado de aquellos materiales que fueran conductores. Con esa idea nació el proceso de electroerosión en 1943. Los Lazarenko perfeccionaron dicho proceso y diseñaron un circuito que llevaba su nombre y que consistía en una sucesión de descargas que se producían entre dos conductores separados entre sí por una película de líquido no conductor llamado dieléctrico. Hoy en día, sin embargo, muchas máquinas de electroerosión utilizan una versión avanzada del circuito Lazarenko.
PERSPECTIVAS FUTURAS:
Una empresa utilizadora de este proceso, ONA ELECTROEROSION, ha estado realizando investigaciones sobre cómo poder mejorar este tipo de proceso.
El CNC de la familia de máquinas de corte de electroerosión por hilo ONA CS y HS incorpora como principales novedades:
Tablas tecnológicas y estrategias especializadas para ranuras. Es posible realizar ranuras de gran profundidad (superiores a 100 mm) con las máxima garantías de calidad y precisión.
Tablas tecnológicas para superficies, específicamente desarrolladas para obtener una rugosidad final excelente y homogénea en superficies grandes de trabajo.
Función "inyección submarina"
EMPRESAS QUE LO UTILIZAN:
Ejemplos de empresas que utilizan este procedimiento serían:
Dongguan Gensun Precision Machining
JURA FILTRATION INDUSTRIE
Goodwill Precision Machinery Co., Ltd (GPM)
NITRURACIÓN
TIPO DE PROCEDIMIENTO:
La nitruración es un proceso de fabricación que consiste en el conformado o deformación plástica del material, conservando su masa. Es un proceso de terminación de piezas que se basa en la formación de una solución sólida de nitrógeno y nitruros en la capa superficial de la pieza de acero. Los nitruros son extremadamente duros, por lo que confieren mucha dureza a la capa superficial de la pieza.
El proceso de nitruración se produce a temperaturas relativamente bajas (500-600°C), y en un medio amoniacal que al descomponerse desprende nitrógeno elemental capaz de reaccionar con el metal.
MATERIALES EN LOS QUE SE UTILIZA:
Normalmente se emplean aceros entre 0,2 y 0,60 % C, aleados con Al, Cr, Mo y V. El contenido de C no influye en la dureza y levemente en la profundidad de capa, disminuyendo ésta con el % de C.
El Al es el elemento más importante para lograr las máximas durezas, pero debe ir siempre acompañado de otros aleantes para evitar capas nitruradas muy frágiles.
El Mo aumenta la dureza de la capa, mejora la tenacidad del núcleo y evita la fragilidad de los aceros sin Mo, cuando permanecen mucho tiempo a temperaturas próximas a 500° C.
El Cr y el V aumentan la profundidad de capa dura.
En los aceros al carbono, a igualdad de tiempo, se obtiene una mayor profundidad de capa, ya que los aleantes forman nitruros y disminuyen la difusión hacia el interior, pero los valores de dureza son sensiblemente inferiores.
TIPO DE PIEZAS QUE SE OBTIENEN:
La nitruración se aplica principalmente a piezas que son sometidas regularmente a grandes fuerzas de rozamiento y de carga, tales como pistas de rodamientos, camisas de cilindros, árboles de levas, engranajes sin fin, etc. Estas aplicaciones requieren que la piezas tengan un núcleo con cierta elasticidad, que absorba golpes y vibraciones, y una superficie de gran dureza que resista la fricción y el desgaste.
Las piezas que se hayan pasado por un proceso de nitruración se pueden usar en trabajos con temperaturas de hasta 500 °C (temperatura de nitruración), temperatura a la cual el nitrógeno comienza a escaparse de la pieza, eliminando los efectos de la nitruración y disminuyendo la dureza de la pieza.
Las aplicaciones habituales incluyen engranajes, cigüeñales, árboles de levas, seguidores de levas, piezas de válvulas, resortes, tornillos de extrusión, herramientas de fundición, troqueles de forja, matrices para extrusión de aluminio, inyectores y moldes de plástico.
MAQUINARIA NECESARIA:
La nitruración puede ser en horno gaseoso, en baño de sales fundidas o iónica. Si nos centramos en el primer caso, la pieza se introduce en un horno en el que se llena la atmósfera con amoníaco y luego se calienta a temperaturas de aproximadamente 500°C. Esto hace que el amoníaco se descomponga en nitrógeno e hidrógeno; el hidrógeno se separa del nitrógeno por diferencia de densidad y el nitrógeno, al entrar en contacto con la superficie de la pieza, forma un recubrimiento de nitruro de hierro.
IMPACTO AMBIENTAL:
Este tratamiento termo-químico puede hacerse por baño de sales, gaseosa o plasma, este último presenta bastantes ventajas; entre ellas se puede mencionar el bajo impacto ambiental que permite un alto control sobre las variables de proceso, logrando controlar los espesores de la capa compuesta y la exterior lo que nos garantiza la repetitividad y la exactitud de las propiedades obtenidas.
ANÁLISIS HISTÓRICO:
La acción endurecedora que el nitrógeno ejerce sobre el hierro y los aceros fue descubierta por Fermi hacia el año 1861, cuando experimentaba la acción del amoniaco sobre piezas de acero calentadas a elevadas temperaturas.
A pesar del gran interés que parecía tener el proceso, pasaron muchos años sin que este método se pudiera aplicar industrialmente con éxito, debido a la fragilidad con la que quedaba la capa superficial de los aceros nitrurados.
En 1905, el francés Hjalmar Braune anunció que en sus trabajos había descubierto la existencia de un eutectoide , parecido a la perlita, formado por hierro y nitruro de hierro FE4N en las capas frágiles de los aceros nitrurados. A este eutectoide se llamó braunita en recuerdo a su descubridor.
Después de terminada la primera guerra europea, en el año 1923, el doctor Fry
de la casa Krupp, descubrió que el problema de fragilidad de la capa exterior de las
piezas nitruradas podía ser resuelto empleando una temperatura de nitruración
relativamente baja (unos 500 ºC aproximadamente) y con el uso de aceros aleados con
aluminio, cromo y molibdeno en lugar de aceros ordinarios al carbono. Si se realiza el
proceso a temperaturas muy próximas a 500 ºC no aparece braunita en la capa
superficial, como ocurre cuando el tratamiento se realiza a temperaturas elevadas y
como normalmente se venía haciendo hasta que Fry realizó sus investigaciones.
PERSPECTIVAS FUTURAS:
Se ha inventado recientemente una novedosa tecnología aplicada a este proceso (la nitruración iónica asistida por plasma de arco eléctrico), para lo que se adaptó un equipo industrial (Deposición Física en fase Vapor o PVD, por sus siglas en inglés) con el fin de mejorar estos procesos termoquímicos. Como fruto de este trabajo, realizado en las instalaciones de la Asociación de la Industria Navarra (AIN), se han obtenido patentes registradas a nivel nacional y europeo.
El tratamiento termoquímico, con el equipo industrial adaptado, lo aplicó Fernández al acero “maraging”. “Se trata de un singular tipo de aleaciones, que se usan, sobre todo, en el ámbito de la industria aeronáutica y aeroespacial y son también de aplicación en herramientas de conformado y moldes. Incluso en la industria del ocio han tenido una cierta acogida, ya que se pueden encontrar palos de golf o armas de esgrima fabricadas en acero ‘maraging’, siempre en artículos de altas prestaciones y alto valor añadido”
EMPRESAS QUE LO UTILIZAN:
Ejemplos que se pueden citar de empresas que usan este método son:
TECMA SRL
BILTRA
FUENTES UTILIZADAS:
https://www.grupotordesillas.net/dureza-acero-upna/
http://www.biltra.com/tratamientos-termicos/nitruracion/
http://kuzudecoletaje.es/tratamientos-termicos-de-los-metales-la-nitruracion/
https://es.wikipedia.org/wiki/Nitruraci%C3%B3n
https://www.lincolnelectric.com/es-es/support/welding-how-to/Pages/plasma-cutting-basics-detail.aspx
https://es.wikipedia.org/wiki/Corte_por_plasma#Equipo_necesario
http://www.gestiondecompras.com/es/productos/conformado-de-chapa/corte-por-plasma
http://www.kjellberg.de/Tecnologia-de-corte/Plasma/Procedimiento/Gases-utilizados.html
https://blogs.nippongases.es/blog/corte-plasma/
https://barmalopesa.com/categoria-producto/soldadura/corte-por-plasma/
Perfecto. Entrada muy completa. Procedimientos bien elegidos. Todos los apartados están muy bien redactados. Mencionas la robotización como futuro del corte por plasma (muy bien) y también el control numérico en la electroerosión por hilo (perfectamente explicado).
ResponderEliminarMuy interesante todo lo que explicas sobre la nitruración (un procedimiento específico de la industria del acero).
Muy bien todas las referencias y las imágenes. Todos los enlaces funcionan. Solo me queda una duda: ¿quién es Fernández?